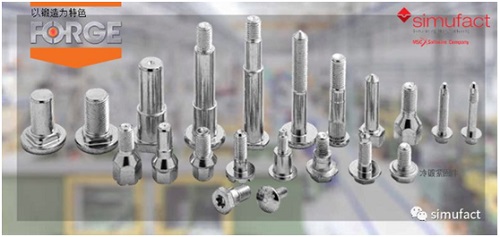
通过有限元仿真技术对紧固件的冷锻过程进行建模和工艺过程的预测性分析。在这个案例中,我们对在车轮螺栓锻造中使用的冲头进行了重新考虑和设计,以消除在锻件空心截面处出现冲头“粘附”的情况。
有限元模拟在过去十年间,在我们这一行业中的角色变得日益重要,这归功于它在所有应用学科特别是在金属成型作业中展现出的精准预测能力。金属成型仿真能减少这类研究中所需的大量物理测试,可用于开发出独特的加工工艺,与此同时,金属成型仿真也广泛用于行业中的预测性监测,比如潜在材料损坏的预测、锻造力监测、最佳的模具设计以及行业中的拓扑优化。
仿真在对成本产生影响的同时,也使人们在生产中变得更轻松。例如,通过在办公室中的数值模拟提高模具的使用寿命可以降低工人进行模具更换操作的次数。
与热锻相比,冷锻中材料的流动性较差。因此,模具设计需要设计者拥有丰富的经验,能够在设计阶段,在有限元仿真的帮助下预测可能出现的问题。本文表明,尽管尽了最大努力,且将完整的工艺设计与有限元模拟相结合,仍然可能出现无法预测的工艺缺陷。然而,令人惊讶的是,通过使用金属成型工艺仿真工具Simufact.forming,我们可以找到出现这些缺陷的原因并进行消除,这表明了工程软件对于锻造工业的影响。
车轮螺栓锻造中的一个出乎意料的问题
由于压力会使零件产生严重的塑性形变,因此冷锻工艺的设计在螺栓制造中至关重要,它能实现在不浪费任何材料的情况下极大地强化材料性能。然而,零件材料从室温下经过锻造后,材料在变形期间可能处于断裂强度的临界线上。尽管所有教科书中都提到了这种类型的材料锻造问题,然而失效也可能出现在整个模具系统中。本文的主题就是关于这方面的一个例子。
在生产M12x1.5x12车轮螺栓的过程中,在锻造的第四阶段会出现冲头损坏的情况,因此我们需要增加冲头的数量,以完成指定数量的紧固件生产。在第三阶段,螺栓头被加工成六角形,在锻造的第四阶段,螺栓头的六角形和空心截面同时成型至最终尺寸(图1)。此处,我们可以看到冲头粘附在成型后的螺栓的空心截面上,这可能是在锻造工序中拔出冲头时造成的,随后冲头断裂(图2)。锻造模具系统包括静止和移动的模具。移动模具系统包括一个能够使六角螺栓头发生变形并使冲头穿过半螺栓的模具弹簧。
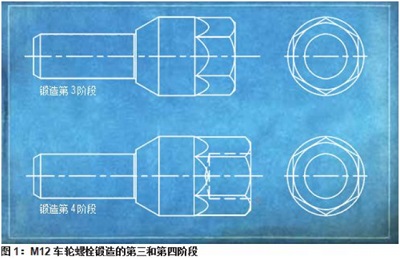
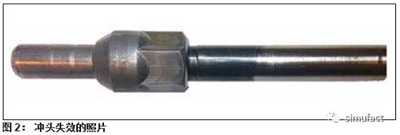
仿真对于冷锻设计的影响
在变形完成时,六角模具和冲头同时向相反的方向移动,然后拔出。在这一点上,理解工艺过程中的材料流动非常关键。许多金属成型仿真软件包在其软件库中含有锻造模具弹簧,但是对弹簧运动进行精准建模却无法实现的。而在Simufact.forming中通过将具体的模具运动界定为时间函数,可以更加轻松地模拟复杂的模具运动。
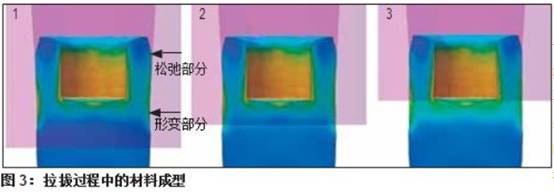 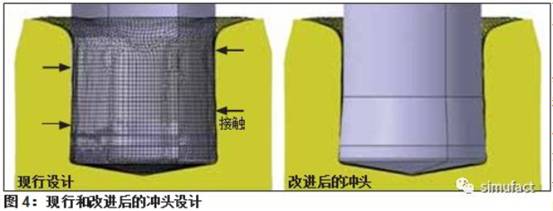
我们对这四个阶段的锻造过程进行了有限元仿真。首先,在无冲头的情况下对锻造的第四阶段(成型和拉拔操作)进行建模分析,以确定孔径减小的情况(图3)。六角模具由一个形变部分和一个松弛部分组成。当通过形变部分锻造材料时,模具壁形成角度,以降低松弛部分中流动的材料和模具之间的摩擦。这使得材料更易于流动。人们可以看到,在拉拔过程中形变部分正在推动材料,然而,这会导致车轮螺栓锻造过程中螺栓孔直径的下降。因此,介于11.01 -11.05 mm之间的孔径世纪会下降至约10.62 mm。这导致冲头与材料之间的接触压力大大增加。
在到达临界点之后,由于压力的升高,冲头无法在空腔中移动,并由于较高的张应力而发生断裂。为了消除这一现象,考虑到孔径的预定下降,我们改进了冲头的几何形状,如图4所示。通过Simufact.forming得到的预测结果显示,材料与冲头之间的接触压力降下来了。
这使得材料更易于流动。人们可以看到,在拉拔过程中形变部分正在推动材料,然而,这会导致车轮螺栓锻造过程中螺栓孔直径的下降。因此,介于11.01 -11.05mm之间的孔径世纪会下降至约10.62 mm。这导致冲头与材料之间的接触压力大大增加。
在到达临界点之后,由于压力的升高,冲头无法在空腔中移动,并由于较高的张应力而发生断裂。为了消除这一现象,考虑到孔径的预定下降,我们改进了冲头的几何形状,如图4所示。通过Simufact.forming得到的预测结果显示,材料与冲头之间的接触压力降下来了。
验证解决方案
有限元仿真使锻造工艺设计者无需在车间进行试错试验便可以进行他们的解决方案的虚拟验证。
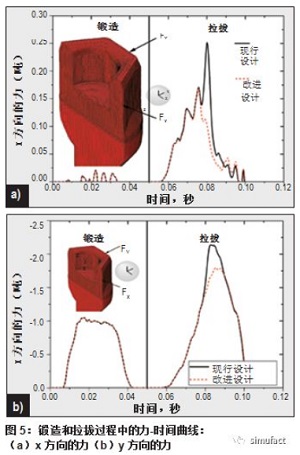
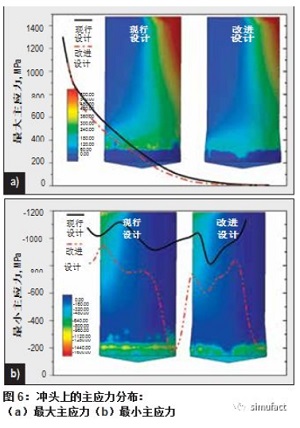
为证明改进设计,并和原有方案进行重要的机械变量(例如锻造力和产生的应力)的对比,该方法被应用于新的仿真模型中,我们将现行设计和改进设计的锻造力进行了比较,如图5a和5b所示。可以假设,在x和y轴方向上的锻造力是造成半螺栓孔中冲头卡住的主要原因。如图5a和5b所示,尽管改进设计未改变在螺栓成型期间力的曲线。但在拉拔期间,在锻件上所受到的力呈下降趋势。这表明,改进后的冲头不会再承受导致其塑性变形至断裂的高拉拔力载荷。
多亏了先进的仿真软件,我们可以针对模具系统中的指定部件进行应力分析。众所周知,使用弹性模具进行成型仿真需要强大的计算能力和较长CPU运行时间。然而,在工业中,时间是一个关键量,不能浪费。
在Simufact.forming中进行成型过程仿真,用户无需使用弹性模具进行3-D仿真来确定在锻件和冲头上的应力分布。特殊的模具应力分析模块使用户可以施加前一步通过使用刚性模具进行仿真计算而得的锻造力,并将这些载荷施加在弹性模具上。通过这种方式,CPU运行的时间大大缩短。
通过使用该模块,我们确定了在改进设计的冲头上的最大和最小主应力的分布,并与现行设计进行了对比,如图6a和6b所示。我们沿冲头表面的边缘路径收集到了应力值。这些应力值的分布对于确定冲头的疲劳寿命至关重要。可以看出,采用新冲头的设计,应力值大大降低。
结论
本文针对在车轮螺栓锻造过程中出现的一个独特问题,阐述了在冷锻应用中使用有限元模拟的重要性和高效性。花费一点时间准备和进行仿真可以大大降低人工和设计的工作量、在锻压机上浪费的时间、所消耗的能量以及试验成本。根据所得到的数值结果,我们制造了新的冲头并进行了锻造试验,该试验表明仿真结果与实际应用一致。仅需要一天的数值计算工作,我们就可以通过冷锻成功制造出车轮螺栓。此外,相比于以往的设计,锻件寿命提高了四倍。
|